Elastomer processing
A rubber compound consists of a large number of components that should be mixed as homogeneously as possible in a mixing process. Frequently, several rubbers are mixed together to form a blend in addition to one rubber. The aim is to achieve defined, application-relevant properties for special applications. The application-relevant properties of an elastomer component are fundamentally dependent on the manufacturing process. Technological and material factors influence the quality of the mixture. We are happy to support you in research projects and advise you on the design of the compound formulation and the mixing parameters.
In the discontinuous mixing process, we can produce mixtures (~ 50 to 60 g) for you and examine them with regard to the vulcanisation kinetics and the mechanical and viscoelastic properties.
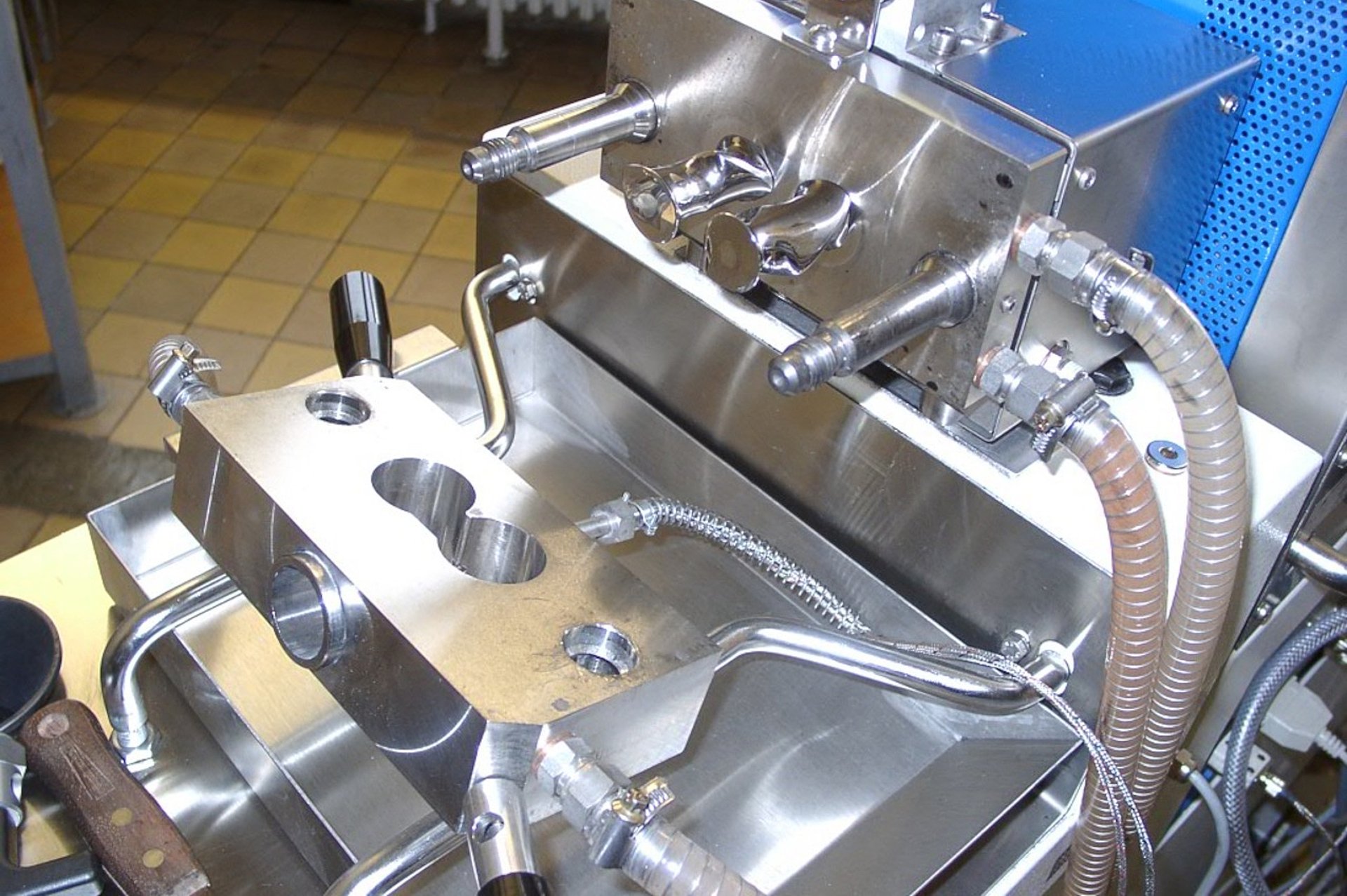
Fundamentals
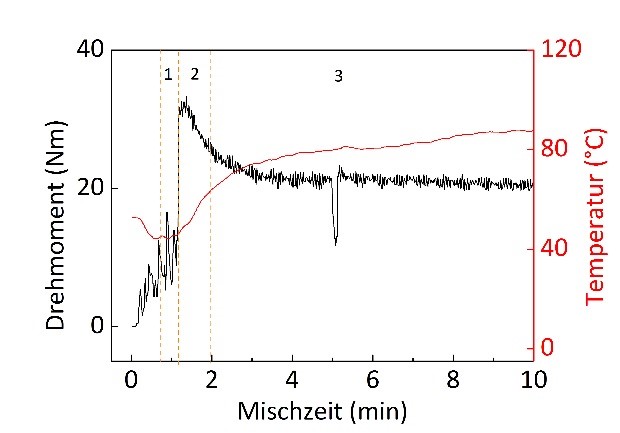
Rubber compounds are mixtures of a large number of components, such as polymers, fillers, plasticisers and various chemicals, which determine the final properties of the vulcanised product. In order to be able to realise a consistent mixing quality, a reproducible mixing process is of great importance.
Mixing is understood as the distribution and division of at least one component in another, whereby the components differ in terms of their properties. Furthermore, a distinction is made between distributive and laminar mixing. In the former, the components are moved against each other by an applied force, so that mixing takes place over time. This is referred to as a static process in which the individual particles do not change their size. We speak of laminar mixing when the components to be mixed are viscoelastic liquids or at least deformable substances.
A rubber mixture consists of a large number of components that should be mixed as homogeneously as possible in a mixing process. The aim of the intended variation of the mixture components is to obtain defined, application-relevant properties for special applications.
At the beginning of the mixing process, rubber, filler, plasticiser, as well as auxiliary materials and additives are filled into the internal mixer at different times. As soon as the mixing chamber is closed by lowering the plunger, the mixing process begins. The pressure acting on the mixture components increases, which leads to a rise in temperature. The polymer becomes more flowable and begins to fill the cavities of the filler (infiltration). Polymer-filler agglomerates form, which lead to an increase in viscosity. As a result of acting compressive, shear and tensile stresses during mixing, the larger filler agglomerates are broken down into smaller aggregates, which are dispersed (dispersion) and distributed (distribution) in the polymer matrix as mixing time progresses. If the effective stresses fall below a critical value due to a strong reduction in viscosity as a result of an increase in temperature or polymer degradation, then the comminution of the agglomerates decreases.
The time of filler incorporation and dispersion can be followed on the basis of the course of the torque-time curve. After lowering the ram, an increase in torque can be observed up to a maximum (area 1). Up to this point, the mixture components are mixed. The filler surface is wetted by the polymer chains during this phase. When the torque reaches its maximum (range 2), the filler is fully incorporated into the polymer matrix. This torque maximum is also called "Black Incorporation Time (BIT)".
Technical equipment
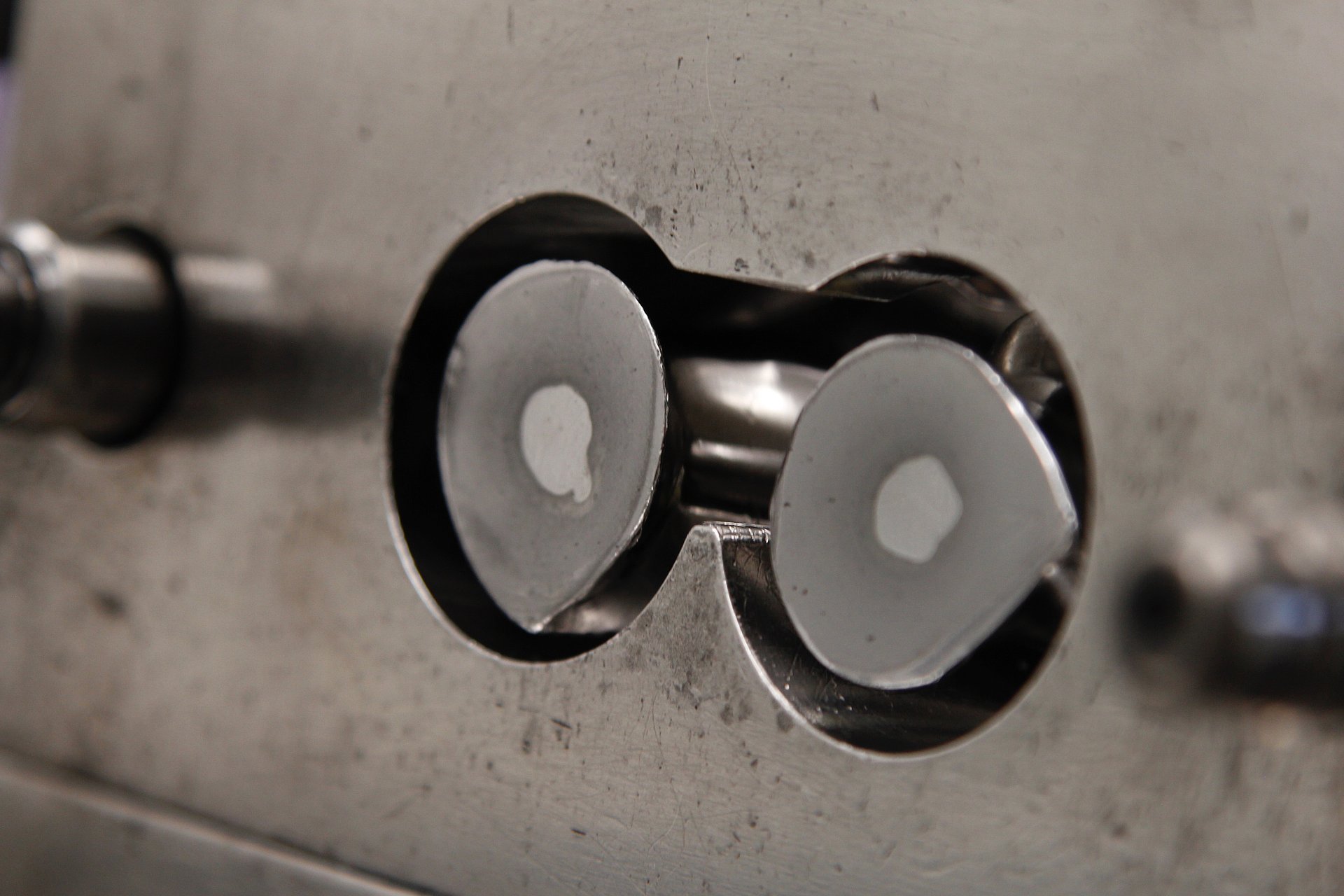
Laboratory internal mixer
- Chamber volume: 75 cm³
- Kneading blades: Banburry
- Temperature: up to 300 °C
- Maximum torque: 40 N
- Recording of torque-time and temperature-time diagrams for mixture production
- Reproducible determination of the Black Incorporation Time (BIT) according to Cotten
- Creation of temperature-corrected torque-time curves
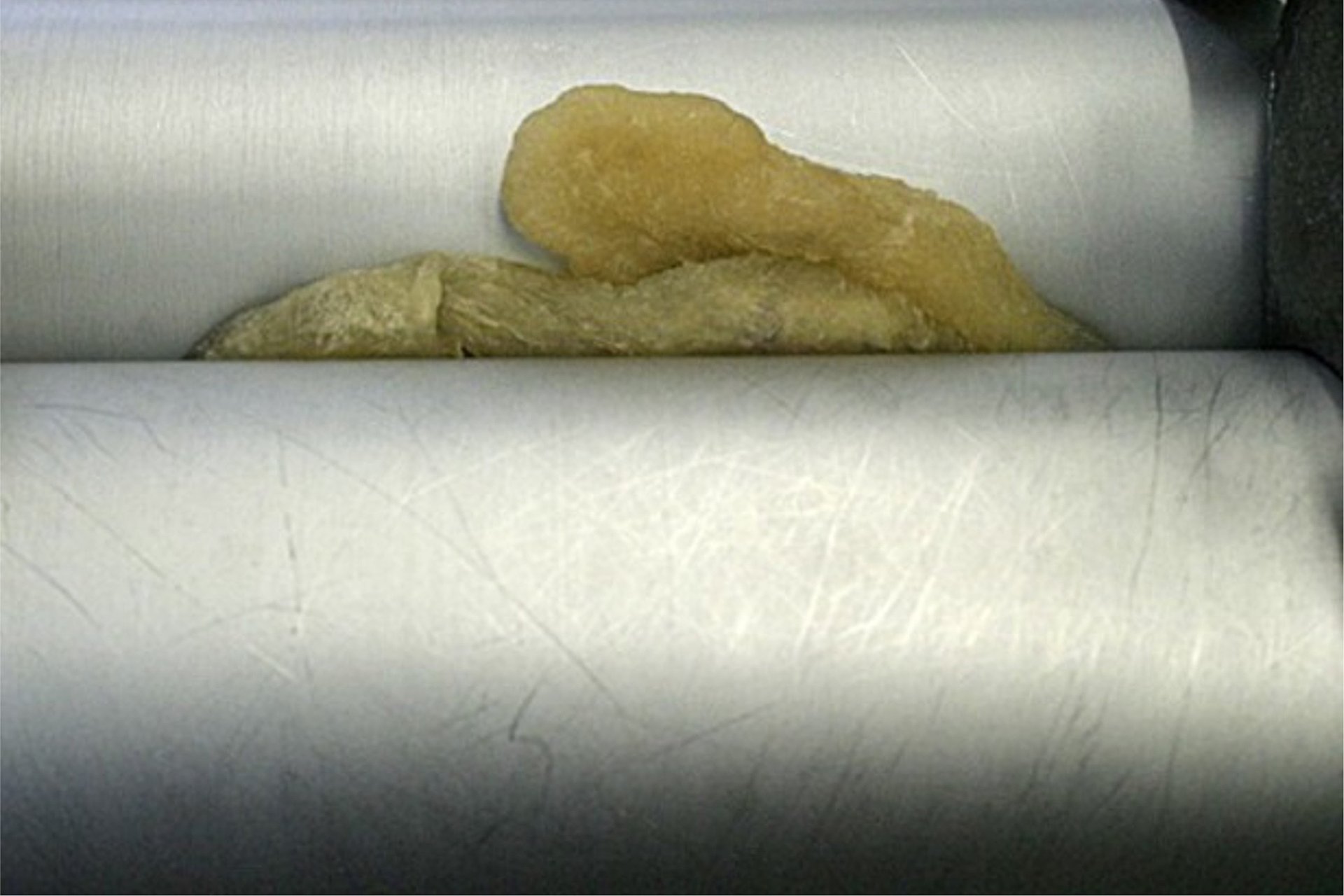
Laboratory mill
- Homogenization and compounding of rubber mixtures
- Mechanical-thermal stress and activation of rubber powder
Dr. Katja Oßwald
Phone: +49 (0)3461 30889-72
Write e-mail